Pseudo motor API reference
A pseudo motor has a state
, and a position
attributes. The state
indicates at any time if the pseudo motor is stopped, in alarm or moving. The
state is composed from the states of all the physical motors involved in the
pseudo motor. So, if one of the motors is in moving or alarm state, the whole
pseudo motor will be in that state. The position, indicates the current
position.
The other pseudo motor’s attributes are:
drift correction
Flag to enable/disable drift correction while calculating physical motor(s) position(s). When enabled, the write sibling(s) position(s) will be used, when disabled, the read sibiling(s) position(s) will be used instead. By default drift correction is enabled. For more details, see Drift Correction.
siblings
List of other pseudo motor objects that belongs to the same controller.
The available operations are:
start move absolute
Starts to move the pseudo motor to the given absolute position.
stop
Stops the pseudo motor motion, by stopping all the physical motors, in an orderly fashion.
abort
Stops the pseudo motor motion, by stopping all the physical motors, as fast as possible (possibly without deceleration time and loss of position).
release
Release hung motion e.g. due to the hardware controller that got hung. You should first try stop/abort.
See also
- Pseudo motor overview
the pseudo-motor overview
PseudoMotor
the pseudo-motor tango device API
PseudoMotor position
The pseudomotor’s current position can be obtained by reading the position attribute. The diagram shows the internal sequence of calls. As it is shown on this picture this process is divided into two parts. First the physical motor positions are read from the hardware. Later these motor positions are used to calculate the pseudo position.
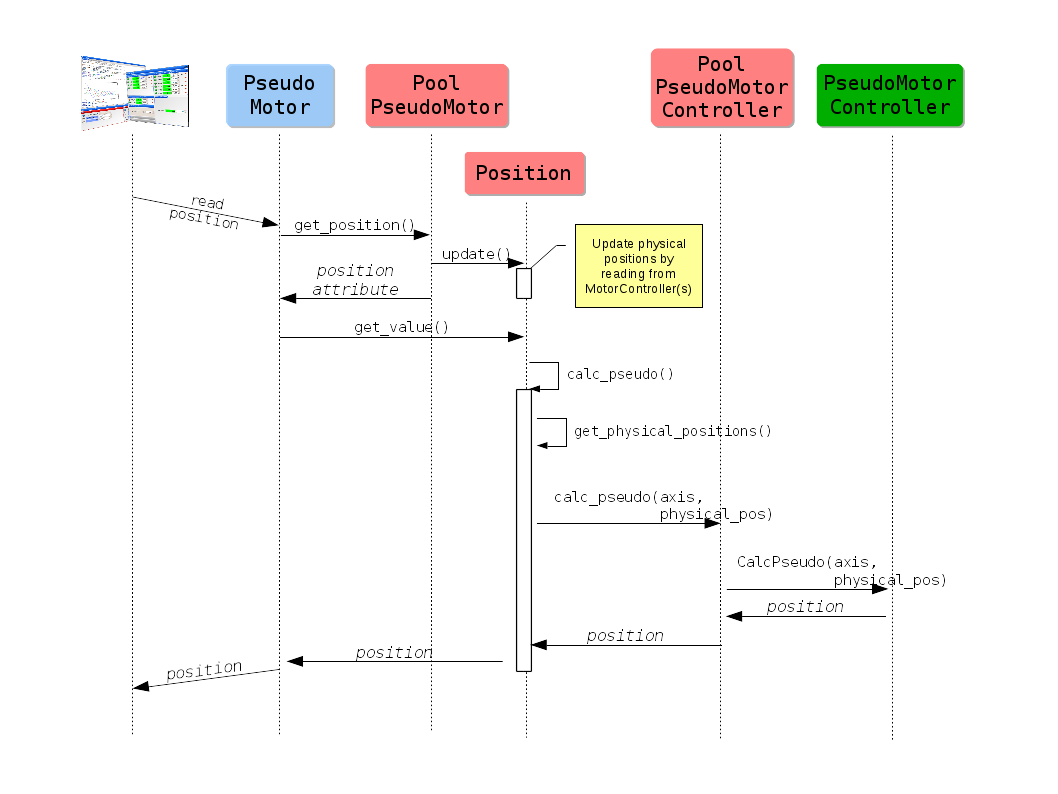
Motion
The most useful thing to do with a pseudo motor is, of course, to move it. To move a pseudo motor to another absolute position you have to write the value into the position attribute.
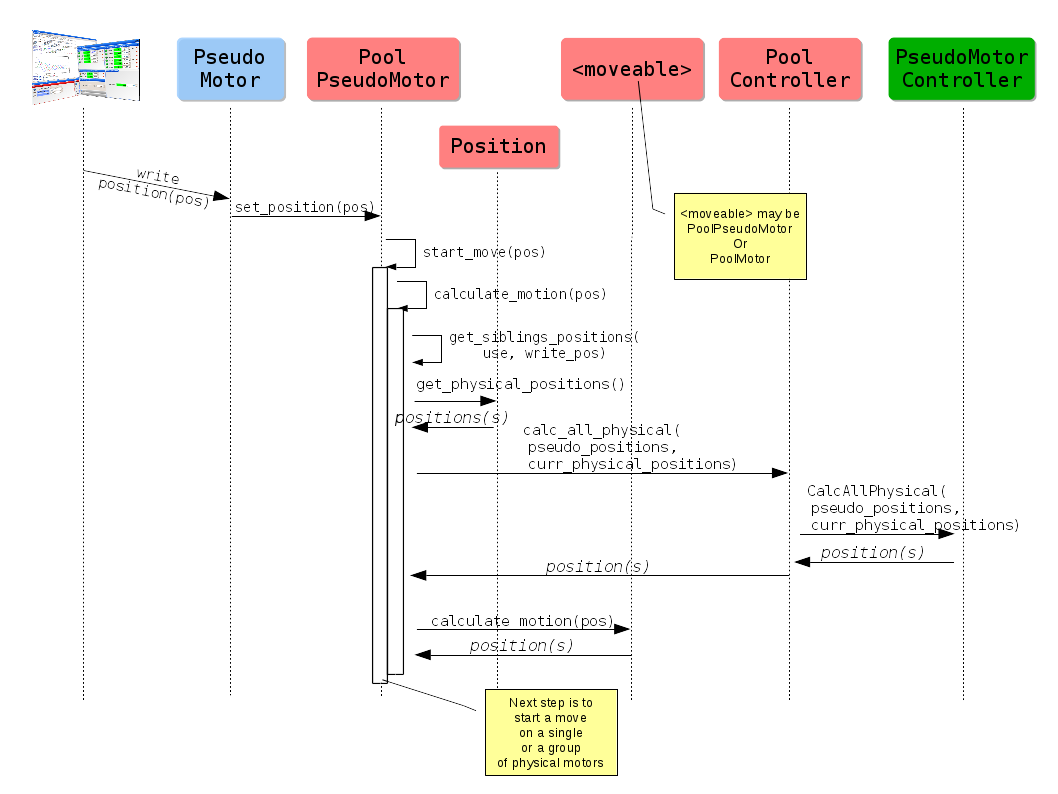
Please refer to
get_siblings_positions()
for more details about use
and write_pos
arguments. The value of the
last one corresponds to the drift correction
attribute value.
After all calculations are done, the pseudo motor will deploy a motion job into the sardana kernel engine which will trigger a series of calls to the underlying motor(s) controller.
Drift correction
Pseudomotors which have siblings and are based on physical motors with an inaccurate or a finite precision positioning system could be affected by the drift effect.
Why does it happen?
Each move of a pseudomotor requires calculation of the physical motors positions in accordance with the current positions of its siblings. The consecutive movements of a pseudomotor can accumulate errors of the positioning system and cause drift of its siblings.
Who is affected?
Inaccurate positioning systems which lead to a discrepancy between the write and the read position of the physical motors. In this case the physical motors must have a position sensor e.g. encoder but must not be configured in closed loop (in some special cases, where the closed loop is not precise enough, the drift effect can be observed as well). This setup can lead to the situation where write and read values of the position attribute of the physical motors are different e.g. due to the loosing steps problems or the inaccurate step_per_unit calibration.
Finite precision physical motors e.g. stepper is affected by the rounding error when moving to a position which does not translate into a discrete number of steps that must be commanded to the hardware.
How is it solved in Sardana?
Sardana implements the drift correction which use is optional but enabled by default for all pseudomotors. It is based on the use of the write value, instead of the read value, of the siblings’ positions, together with the new desired position of the pseudomotor being moved, during the calculation of the physical positions. The write value of the pseudomotor’s position gets updated at each move of the pseudomotor or any of the underneath motors.
Note
Movements being stopped unexpectedly: abort by the user, over-travel limit or any other exceptional condition may cause considerable discrepancy in the motor’s write and read positions. In the subsequent pseudomotor’s move, Sardana will also correct this difference by using the write instead of read values.
The drift correction is configurable with the DriftCorrection property either globally (on the Pool device level) or locally (on each PseudoMotor device level).
Example
Let’s use the slit pseudomotor controller to visualize the drift effect. This controller comprises two pseudomotors: gap and offset, each of them based on the same two physical motors: right and left. In this example we will simulate the inaccurate positioning of the left motor (loosing of 0.002 unit every 1 unit move).
Drift correction disabled
Initial state: gap and offset are at positions 0 (gap totally closed and offset at the nominal position)
Door_lab_1 [1]: wm right left gap offset right left gap offset User High Not specified Not specified Not specified Not specified Current 0.000 0.000 0.000 0.000 Low Not specified Not specified Not specified Not specified
Move gap to 1
Door_lab_1 [2]: mv gap 1
The calculation of the physical motors’ positions gives us 0.5 for both right and left (in accordance with the current offset of 0)
Door_lab_1 [3]: wm right left gap offset right left gap offset User High Not specified Not specified Not specified Not specified Current 0.500 0.498 0.998 0.001 Low Not specified Not specified Not specified Not specified
We observe that the gap pseudomotor did not reach the desired position of 1 due to the left’s positioning problem. Left’s position write and read discrepancy of 0.002 causes that the gap reached only 0.998 and that the offset drifted to 0.001.
Move gap to 2
Door_lab_1 [4]: mv gap 2
The calculation of the physical motors’ positions gives us 1.001 for right and 0.999 for left (in accordance with the current offset of 0.001).
Door_lab_1 [5]: wm right left gap offset right left gap offset User High Not specified Not specified Not specified Not specified Current 1.001 0.997 1.998 0.002 Low Not specified Not specified Not specified Not specified
We observe that the gap pseudomotor did not reach the desired position of 2 due to the left’s positioning problem. Left’s position write and read discrepancy of 0.002 causes that the gap reached only 1.998 and that the offset drifted again by 0.001 and the total accumulated drift is 0.002.
Move gap to 3
The calculation of the physical motors’ positions gives us 1.502 for right and 1.498 for left (in accordance with the current offset of 0.002).
Door_lab_1 [6]: mv gap 3 Door_lab_1 [7]: wm right left gap offset right left gap offset User High Not specified Not specified Not specified Not specified Current 1.502 1.496 2.998 0.003 Low Not specified Not specified Not specified Not specified
We observe that the gap pseudomotor did not reach the desired position of 3 due to the left’s positioning problem. Left’s position write and read discrepancy of 0.002 causes that the gap reached only 2.998 and that the offset drifted by 0.001 and the total accumulated drift is 0.003.
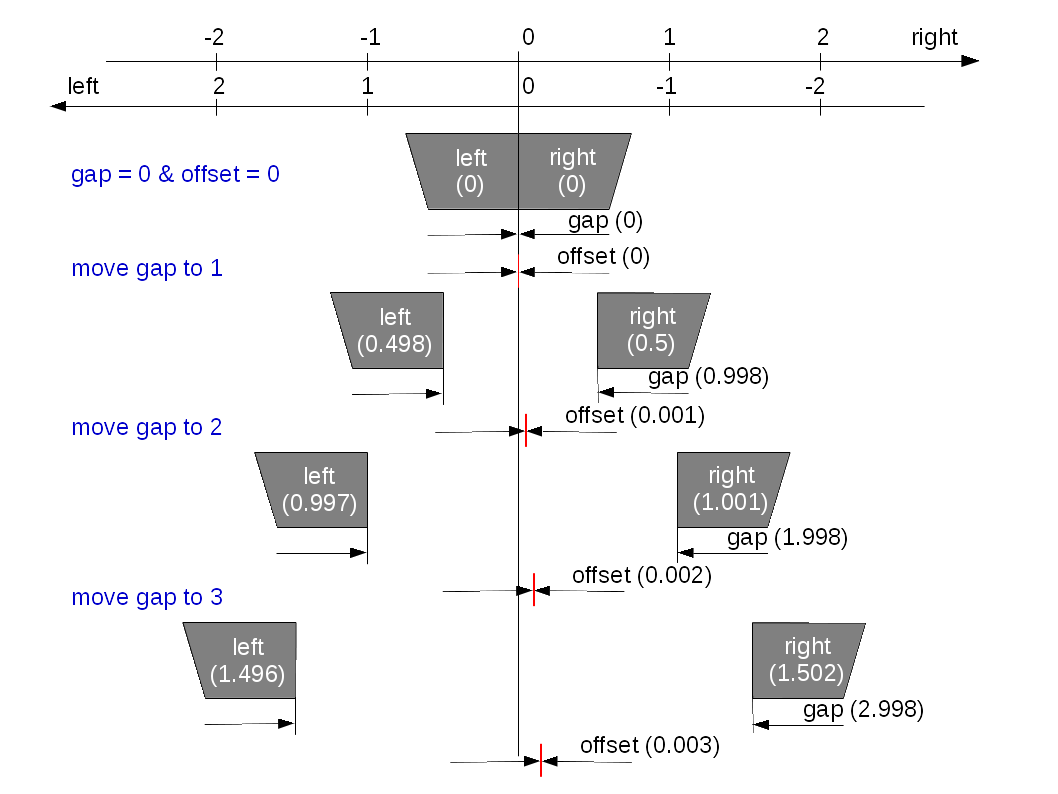
This sketch demonstrates the above example where offset drifted by 0.003.
Drift correction enabled
Initial state: gap and offset are at positions 0 (gap totally closed and offset at the nominal position)
Door_lab_1 [1]: wm right left gap offset right left gap offset User High Not specified Not specified Not specified Not specified Current 0.000 0.000 0.000 0.000 Low Not specified Not specified Not specified Not specified
Move gap to 1
Door_lab_1 [2]: mv gap 1
The calculation of the physical motors’ positions gives us 0.5 for both right and left (in accordance with the last set offset of 0).
Door_lab_1 [3]: wm right left gap offset right left gap offset User High Not specified Not specified Not specified Not specified Current 0.500 0.498 0.998 0.001 Low Not specified Not specified Not specified Not specified
We observe that the gap pseudomotor did not reach the desired position of 1 due to the left’s positioning problem. Left’s position write and read discrepancy of 0.002 causes that the gap reached only 0.998 and that the offset drifted to 0.001.
Move gap to 2
Door_lab_1 [4]: mv gap 2
The calculation of the physical motors’ positions gives us 1 for right and 1 for left (in accordance to the last set offset 0).
Door_lab_1 [5]: wm right left gap offset right left gap offset User High Not specified Not specified Not specified Not specified Current 1.000 0.998 1.998 0.001 Low Not specified Not specified Not specified Not specified
We observe that the gap pseudomotor did not reach the desired position of 2 due to the left’s positioning problem. Left’s position write and read discrepancy of 0.002 causes that the gap reached only 1.998 and that the offset drifted again by 0.001 but thanks to the drift correction is maintained at this value.
Move gap to 3
Door_lab_1 [6]: mv gap 3
The calculation of the physical motors’ positions gives us 1.5 for right and 1.5 for left (in accordance to the last set offset of 0).
Door_lab_1 [7]: wm right left gap offset right left gap offset User High Not specified Not specified Not specified Not specified Current 1.500 1.498 2.998 0.001 Low Not specified Not specified Not specified Not specified
We observe that the gap pseudomotor did not reach the desired position of 3 due to the left’s positioning problem. Left’s position write and read discrepancy of 0.002 causes that the gap reached only 2.998 and that the offset drifted again by 0.001 but thanks to the drift correction is maintained at this value.
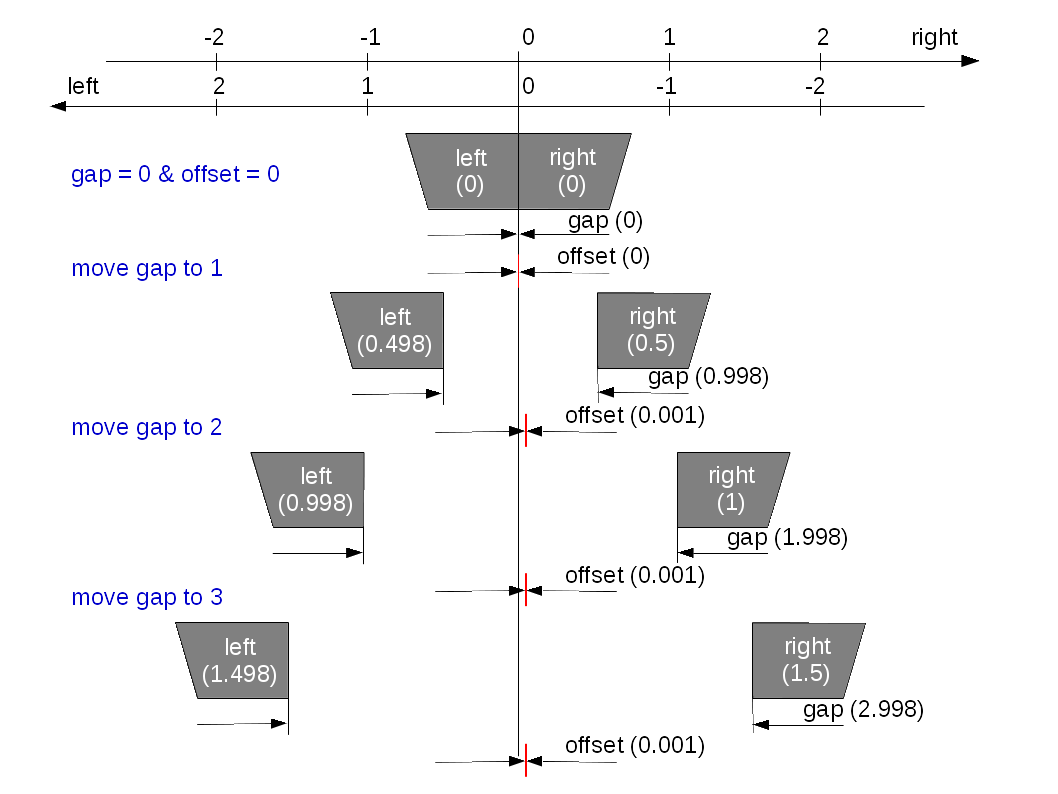
This sketch demonstrates the above example where offset’s drift was corrected.